Why Use Laser Marking Instead of Screen Printing?
Posted on April 1, 2017 in Blogs
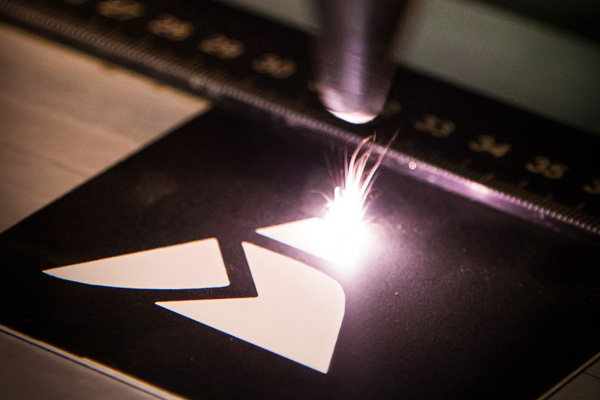
When it comes to marking a surface with a pattern such as a barcode, image, or text, product manufacturers can often choose between laser marking and screen printing (also known as silk screening). Both methods have their advantages depending on the application. Screen-printing, for example, allows for virtually any color pattern (as well as multicolored patterns), while laser marked patterns generally are black, white or shades of gray. Another screen printing advantage is that a wider variety of material can be marked — pretty much anything from tee-shirts to stainless steel, but while laser marking is somewhat more limited, you can laser mark most metals, glass, ceramics, polymers and plastics.
Laser marking offers the following advantages over screen-printing:
- Cleaner and more environmentally friendly (no paints or solvents)
- Faster production (faster setup, faster marking, no cleanup)
- Ability to mark in three dimensions (e.g., round objects)
- Very precise marking (useful on very small objects and in tight spaces)
- More permanent (e.g., markings on a switch or dial won’t rub off after repeated use)
- Can be autoclaved (as when medical or dental instruments are sterilized)
- Less chance of external contamination (there’s no pigment to come off a biomedical implant, for example)
How These Methods Work
With laser marking the pattern results from the laser beam either oxidizes or removes the material, leaving a mark wherever the beam touches the surface. Different patterns are possible depending on where the laser beam is directed by mirrors. Alternatively, the table on which the surface is mounted can move while the position of the laser above it remains fixed.
In screen printing, the pattern is painted on. The way this happens is by a squeegee pressing ink onto the surface as the squeegee moves across the back of an ink-soaked mesh. A stencil attached to the front of the mesh causes the ink to only flow where there are openings in the stencil, thus creating the desired pattern. The name “silk screen” comes from the fact that these meshes once were made only from silk. Today, most meshes are made of polyester, although nylon and stainless steel meshes may also be used in certain applications.
The reasons that laser marking can offer its many advantages are fairly self-evident. Nothing is added to the surface being marked, so there’s nothing to rub off; there’s very little setup to prepare; there’s nothing to clean up; and there’s nothing to contaminate a sterile application (such as a biomedical implant). Turn times can be measured in days instead of the weeks typical of screen printing. Laser light is extremely precise — meaning that it’s possible to create very small markings that are specified to much smaller tolerances than is possible with a stencil. Light is much more easily and effectively directed (versus ink flowing through a mesh and a stencil), so it’s also possible to apply markings in very tight spaces and on three-dimensional objects.
As with all applications, however, the best advice is to consult an expert before committing your particular project to one method or another. Ask about turn times, costs, durability, precision and the other factors that are most relevant to your particular marking needs. Doing a little homework ahead of time is the best way to ensure you’ll know what results to expect, with no surprises later.