Solutions for Laser Welding Various Types of Stainless Steel
Posted on December 14, 2021 in Blogs
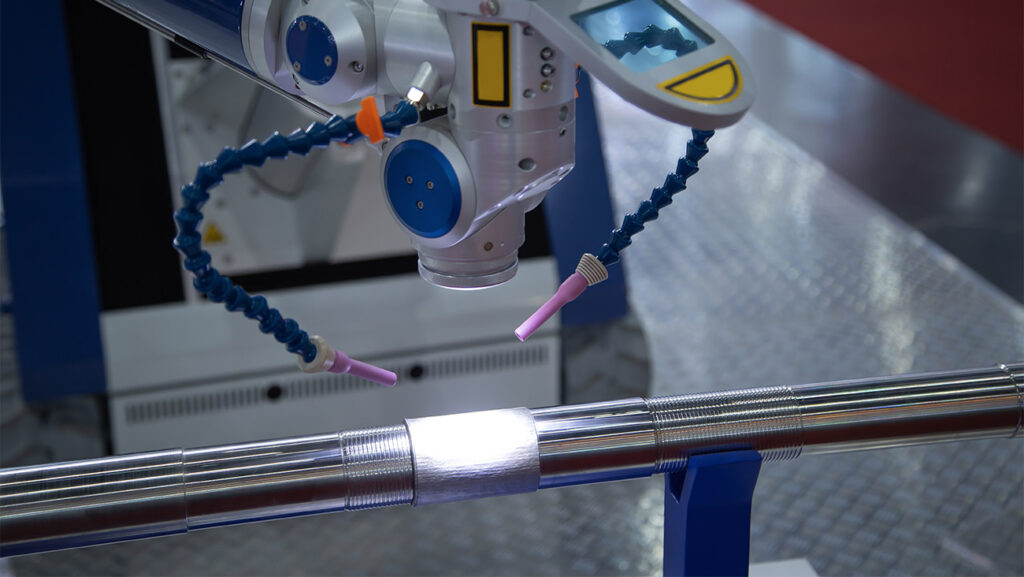
Stainless steel is a material solution used in a wide variety of applications because of its inherent corrosion resistance, high temperature oxidation resistance, and strength. Joining separate stainless steel pieces via a high power welding process is preferred over other methods of welding or adhesion in many automotive, medical, and military and aerospace (MIL/AERO) applications because of laser welded joints offer the highest strength and a variety of other benefits. These include:
- Small HAZ area: Stainless steel joints often need to not only be strong but often cosmetically clean. The laser offers the smallest heat affected zone, or “HAZ.” This also makes laser welding ideal for products with intricate weld patterns, or where the area to be welded is difficult to reach. Because the laser beam can be focused so precisely, there is less likelihood of damaging, pitting, or deforming the surrounding surfaces, as well.
- Clean process: Because the laser welding operation is simply the fusing of metals, there is (typically) no need for filler materials, and there are no additional environmental risks. This oftentimes makes laser welding the most cost-effective and eco-friendly option. And in end products, such as stainless steel tubes used in medical devices and surgical applications, the laser’s overall cleanliness ensures products are delivered free of contaminants and burrs.
- Less corrosion: In conventional TIG or MIG welding, the electrode used for welding contains trace amounts of moisture. The heat of the welding causes the water to decompose quickly, and in doing so, it releases hydrogen that enters the metal causing it to become fragile. Because laser welding does not rely on an electrode to conduct heat, there is no risk of self-inflicted corrosion.
- Precision: The power output, size of weld, depth of weld, speed of weld, and the track of the laser beam on the stainless steel surface are all highly controllable. The result is a very precise weld. The thinnest sheets of stainless can also be laser welded due to this optimal control.
- Reduced Thermal Distortion: An additional benefit from laser welding stainless steel is reduced thermal distortion and residual stresses when compared to conventional welding techniques. This is especially important for stainless steels that have a 50% greater thermal expansion than plain carbon steels.
- Automation: Another benefit of a highly controlled process is that laser welding is highly programmable and robotic. Since it’s easier to automate compared to metal inert gas (MIG)* or tungsten inert gas (TIG)* welding methods, greater repeatability and faster throughput can be achieved.
Understanding the 4 types of stainless steel material
Stainless steel is described according to the material property of each type. These are the laser welding considerations and requirements for each.
- Austenitic stainless steels
The 300 series of stainless steel is austenitic stainless steels. These stainless steels are used in applications requiring corrosion resistance and toughness, and when issues relative t thermal distortion are considerations. The 300 series stainless steels can be found in a wide range of applications in petroleum, transportation, chemical, and power generation industries. These stainless steels are particularly useful in high temperature environments. This series of stainless steel is suitable for both pulsed and continuous wave (CW) laser welding. Laser welding stainless steel provides slightly better weld penetration depths and increased weld speeds when compared to low carbon steels due to the lower thermal conductivity of most austenitic stainless steels. The higher speeds from laser welding are also advantageous in reducing the susceptibility to corrosion caused by the precipitation of chromium carbides at the grain boundaries. Chromium carbides precipitation can occur when the heat input is too high during the welding processes. - Ferritic stainless steels
The ferritic 400 series of stainless steel typically have little to no nickel and do not possess as good laser weldability when compared to the austenitic grades. Laser welding the ferritic stainless steel grades in some cases, impairs joint toughness and corrosion resistance. The reduction in toughness is partially due to the formation of coarse grains in the heat-affected zone and martensite formation, which occurs in the higher carbon content grades. The heat-affected zone may have a higher hardness due to the fast cooling rate, which increases the brittleness. - Martensitic stainless steels
The martensitic 400 series of stainless steel is more challenging to laser weld than the austenitic and ferritic grades. Laser welding high carbon martensitic grades (> 0.15% carbon) can cause the material to be brittle in the heat-affected zone. If martensitic stainless steel with carbon contents above 0.1% are to be welded, then use of an austenitic stainless steel filler material can improve the weld toughness and reduce the susceptibility to cracking but cannot reduce the brittleness in the heat-affected zone. Pre-heating the material before welding or tempering the material at 650-750°C after laser welding will help to reduce the brittleness in the heat-affected zone. - Duplex stainless steels
Duplex stainless steels is a mixture of austenitic-ferritic stainless steels. These stainless steels are characterized by a two-phase microstructure containing austenite and ferrite. The volumetric fractions of austenite and ferrite are roughly equal. The main alloying elements are chromium, nickel, and molybdenum. Duplex stainless steels are usually also alloyed with small amounts of nitrogen. Duplex material is generally weldable with good results.
Note on grades and making final choices: Because of the variety of stainless steel types/grades, Accumet encourages process testing before finalizing a design. Also, the use of free-machining grades should be avoided because these stainless steels contain sulfur that can lead to hot cracking during laser welding.
Outsourcing your stainless steel welding to Accumet
Accumet is a full-service processed materials provider offering laser and machining solutions. Our machines are of the highest caliber and include features such as optical alignment, rotary welding, different power outputs, and the capability to be fixtured to accommodate various shapes and sizes.
Optical alignment offers many benefits, including the ability to line up to an existing weld and repair it, for example. Rotary welding allows for welding both inside and outside stainless steel tubes, and even allows us to weld a tube within a tube. Different power outputs allow for the welding of varying types and thicknesses of materials, which also allows for spot welds and continuous welds, dictated by the materials being welded, as well as the size of the weld. Varying machines allow us to achieve any combinations of power, focus diameter of a beam, pulsed energy, pulse duration, and pulse frequency, amongst other parameters, as specified by your project’s unique requirements. We also offer a one-stop experience for all of your laser cutting, production and assembly needs.
*Accumet is both ISO 9001:2015 and AS9100:2016 certified.