Keys to Perfecting Laser Welded Hermetic Seals – Part 2
Posted on June 13, 2019 in Blogs
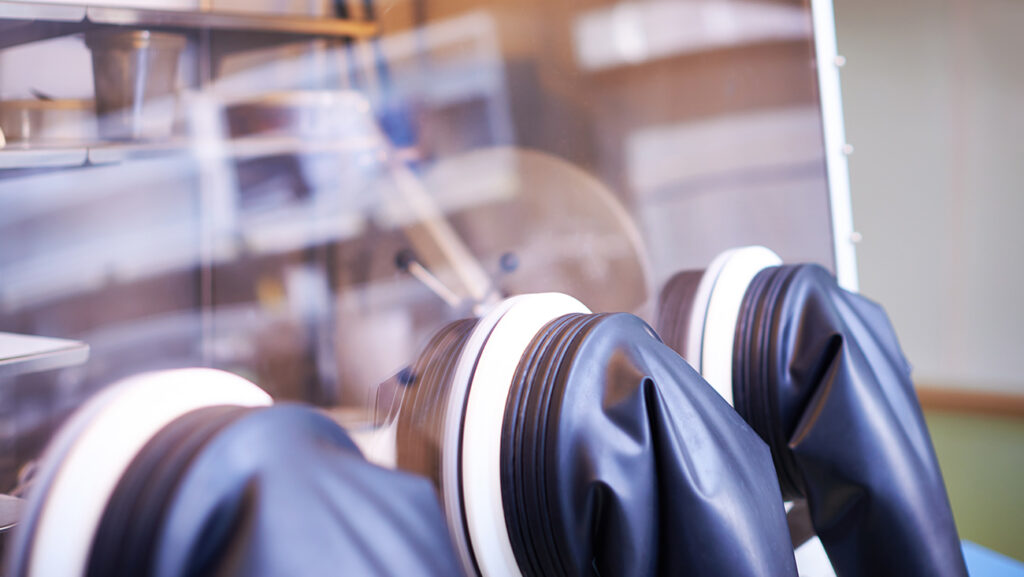
Introduction
In part 1 of this 2-part blog series on laser welding hermetic seals, we presented insight on understanding the materials that are ideally suited for packages, lids, and seals, which laser technology is right for the job, and which laser welded joint types are to best to use.
IV. Consider Final Testing and Potential Rework in Advance
Final testing stages of a hermetically sealed device are necessarily stringent in order to ensure they are application-ready for extended use in harsh environments. As such, even the most visually perfect seal can fail, resulting in removal of the lid, device re-inspection, and re-sealing it. As this is not uncommon, additional overhead and delivery time must be factored in for rework that includes micro-machining of the enclosure to overcome subtle geometric changes to the top of enclosure walls as a result of laser de-lidding. If this is not inspected for and adjusted, the result is poor matchup and future failed tests and rework once again.
The testing and rework stages are determined by the qualifications and certifications necessary to meet with standards associated with the application. For military and space (NASA) applications, a helium leak test (MIL-STD-883 Test Method 1014 for hybrids/microcircuits and MIL-STD-750 Method 1071 for discrete semiconductor devices) is performed to determine the quality of the hermiticity. If found inadequate, a laser welded lid can be removed safely via precision laser cutting. Then the laser welding process is repeated for the seal after the initial cleaning, baking, and fixturing steps are performed.
MIL-STD-750 E, Test Method 1071.9 “Hermetic Seal”
(Equivalent standard leak rates (atm cc/s air) per volume)
• <= 0.002 cc is 5x10e-10 • > 0.002 and <= 0.05 cc: is 1x10e-9
• >0.02 and <= 0.5 cc: 5x10e-9
• >0.5 cc: 1x10e-8
MIL-STD-883H, Test Method 1014.13 “Seal”
(Equivalent standard leak rates (atm cc/s air) per volume)
• <= 0.01 cc: 5x10e-8
• > 0.01 and <= 0.5 cc: 5x10e-9
• >0.5 cc: 1x10e-6
NASA and the U.S. Military are actively investigating the helium leak test effectiveness as a measure of hermiticity, and other hermiticity test methods may be required in the future.
V. Pre-prep Considerations
A. Substrates
While not necessarily impacted by the processing step of laser lidding, due to the fact that your devices will be deployed in critical, long-life applications, it’s important that your ceramic base materials, or substrates, are pre-processed with precision lapping and or polishing to ensure proper flatness, camber, and parallelism. Poor flatness and parallelism of your ceramic material can lead to adhesion and trace/space inconsistencies during circuit metallization (and thus, poor yields), and can create variability in thermal conductivity and electrical insulation across the foundation of your device. Poor camber creates similar electro-mechanical challenges. All can turn into future de-lidding and rework of previously sealed devices.
B. Gases
The inert gases (argon, nitrogen, or helium) used during laser welding depend on material compatibility.
C. Fixturing
Fixturing depends on the joint type and geometries of the enclosure being hermetically sealed. Many aspects, such as time, laser power, materials and pulse duration depend on these pre- prep decisions.
Consider your partner wisely
A laser welding process that produces high-quality, rapid, and low-cost welds can be performed on an extremely wide range of materials and geometries. Hence, laser welding has become one of the choice methods for hermetically sealing electronic packages/enclosures for the devices used in RF/microwave, military, industrial, aerospace, space, medical, and microelectronic applications. Developing a suitable laser hermetic sealing process depends on many factors. Therefore, choosing an experienced laser service partner with a solid track record for hermetic sealing, is also a key decision in meeting and exceeding customer the expectations for the reliability and longevity of your electronics.
Next Steps: Download our Technical Brief “5 Keys to Perfecting Laser Welded Hermetic Seals” to see all 5 of the key steps outlined in this blog series, plus additional support tables and illustrations.