Advancements in Laser Welding Technology: What You Need to Know
Posted on November 19, 2024 in Blogs
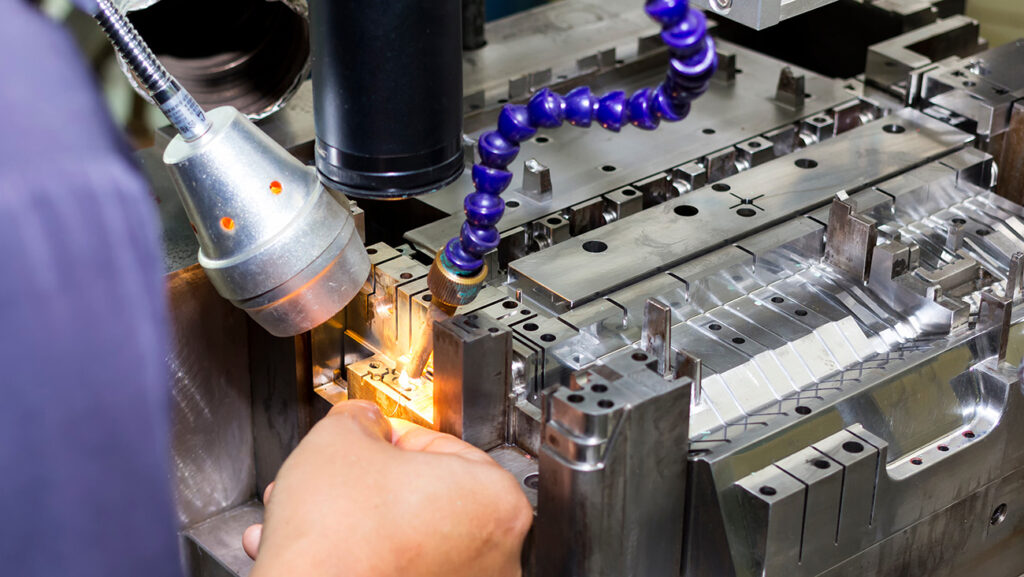
Laser welding technology has made significant strides in recent years, enabling industries to achieve faster, more precise, and stronger welds. As demand grows for reliable and efficient joining methods, understanding the latest advancements can help manufacturers stay ahead of the curve. This article highlights the key innovations in laser welding technology and their implications for various industries.
1. Enhanced Precision and Control
One of the most notable advancements in laser welding is the improvement in precision and control. Modern laser welding systems now offer:
- Smaller beam diameters: Allowing for intricate welds on miniature components.
- Real-time monitoring and feedback: Ensuring consistent weld quality by detecting and correcting anomalies during the process.
- Adaptive welding capabilities: Automatically adjusting parameters to accommodate material variations and complex geometries.
According to Industrial Laser Solutions, these advancements are crucial for industries like aerospace and automotive manufacturing, where precision is paramount.
2. High-Speed Welding Processes
With innovations in laser power and beam delivery systems, welding speeds have increased dramatically. This improvement is especially beneficial for industries like automotive and aerospace, where high-volume production and tight deadlines are common. High-speed welding also reduces thermal distortion, preserving the integrity of the workpiece.
3. Versatile Material Compatibility
Advancements in laser sources, such as fiber lasers and diode lasers, have expanded the range of materials that can be welded effectively. Today’s laser welding systems can handle:
- High-reflectivity metals: Such as copper and aluminum, which were traditionally challenging to weld.
- Dissimilar materials: Combining different metals, like steel and aluminum, is now possible with advanced techniques.
- Heat-sensitive materials: Reduced heat input minimizes damage to delicate components.
4. Automation and Integration
Modern laser welding systems are increasingly integrated with robotic automation, enabling:
- Unmanned operations: Robots handle repetitive tasks with precision, reducing labor costs and human error.
- Seamless production lines: Integration with Industry 4.0 frameworks allows for real-time data sharing and predictive maintenance.
- Customizable setups: Manufacturers can tailor systems to meet specific production needs.
A report by Automation World highlights how integrating automation with laser welding enhances efficiency and productivity.
5. Enhanced Safety Features
Safety is a critical aspect of any welding process. Recent innovations have introduced features such as:
- Enclosed welding cells: Protecting operators from laser radiation and fumes.
- Real-time monitoring systems: Ensuring safe operating conditions and detecting potential hazards.
6. Environmental Benefits
Laser welding technology has become more sustainable, with reduced energy consumption and waste. Some key contributions include:
- Minimized material waste: Precise welding reduces excess material usage.
- Lower energy requirements: Advanced lasers operate efficiently while delivering high power.
- Cleaner processes: Reduced need for consumables, like welding rods and flux, results in fewer emissions.
Applications of Advanced Laser Welding
These innovations are transforming industries such as:
- Aerospace: Lightweight structures and high-strength welds.
- Medical devices: Precision welding of miniature components, ensuring reliability and biocompatibility.
- Automotive: High-speed production of safety-critical components, like batteries and chassis parts.
- Electronics: Joining delicate components with minimal thermal damage.
The advancements in laser welding technology are revolutionizing manufacturing by offering unmatched precision, speed, and versatility. By adopting these cutting-edge systems, manufacturers can enhance productivity, reduce costs, and deliver higher-quality products.
Interested in leveraging advanced laser welding technology for your business? Discover Accumet’s industry-leading laser welding solutions and see how we can support your manufacturing goals.