5 Common Challenges in Laser Machining and How to Overcome Them
Posted on December 17, 2024 in Blogs
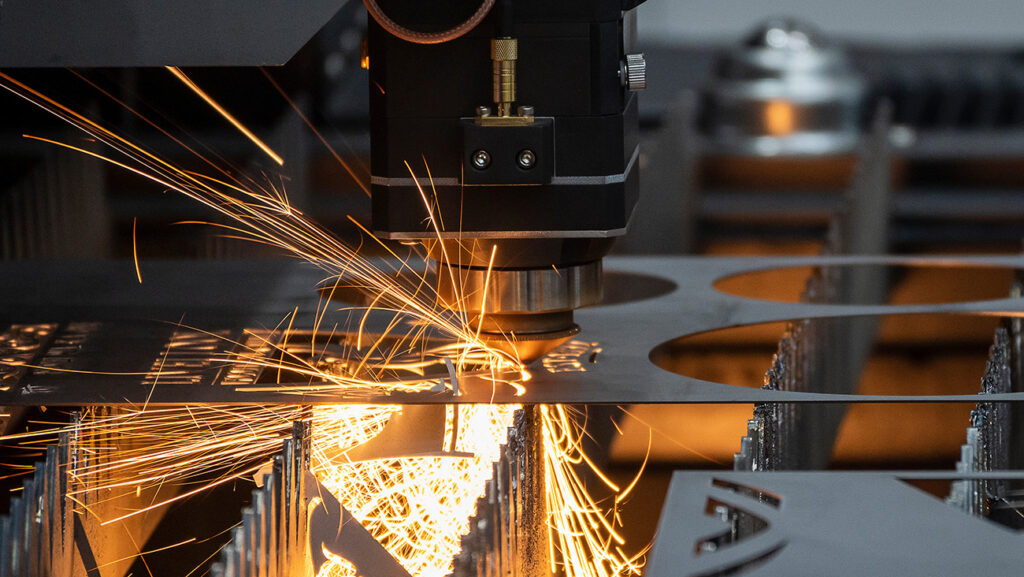
Laser machining is valued for its precision and versatility, but it comes with challenges that can impact production quality. Understanding these issues and how to resolve them ensures efficiency and high-quality results.
1. Thermal Distortion
Excessive heat can cause thermal distortion, especially in thin materials. Using pulsed laser settings and optimizing laser power reduces heat buildup and minimizes warping.
2. Processing Reflective Materials
Highly reflective materials like copper and aluminum are challenging because they reflect laser energy. Fiber lasers, which operate at shorter wavelengths, are better suited for processing these metals.
3. Edge Quality and Burr Formation
Poor edge quality and burrs result from improper laser settings. Adjusting the cutting speed and assist gas pressure produces cleaner cuts with fewer defects.
4. Cutting Thick Materials
Thicker materials require more laser power and slower speeds, which can slow production. Hybrid methods that combine laser and mechanical cutting can improve efficiency for thicker materials.
5. Maintenance and Downtime
Routine maintenance is essential for consistent laser performance. Regular cleaning of optics and system calibration reduces downtime and maintains cut quality.
Overcoming common laser machining challenges requires the right technology, proper maintenance, and optimized settings. Addressing these issues ensures consistent, high-quality results in manufacturing.
Ready to solve your laser machining challenges? Discover how Accumet’s advanced laser machining services can help.